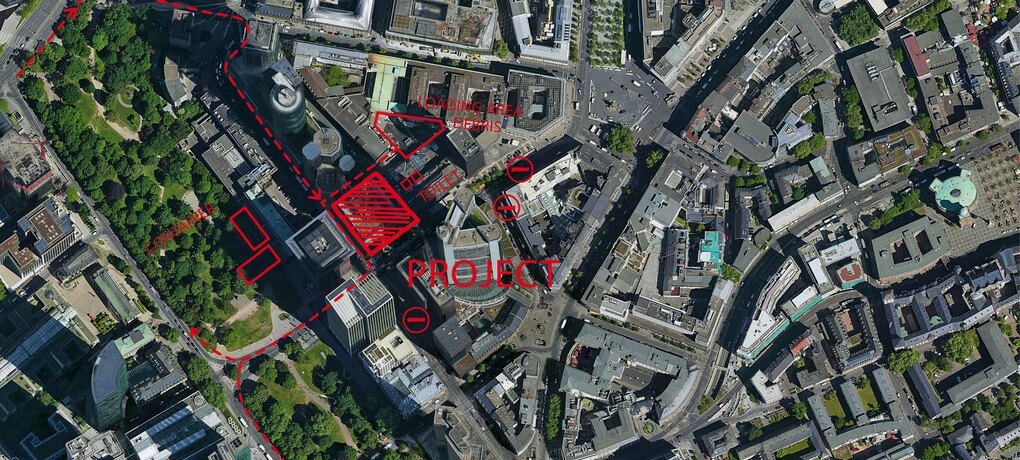
A cure for the chaos on big building sites – state-of-the-art building logistics
Productivity losses due to a lack of organisation are typical of big building sites. In recent years, the new trade of building logistics has developed in order to remedy this. It promises orderly supply and disposal on the construction site, seamless entry controls and structured workflows. This is an ideal addition to modern building logistics and the industrialisation of building technology because pre-fabricated assemblies – like TECEsystem – significantly reduce the complexity of the processes involved.
The urbanisation of living and working is a megatrend all across the world. With the densification of urban construction and transport also comes an increase in the challenges faced in logistics for big building sites. The type of procurement has further worsened the problem: where large projects were awarded in their entirety to general contractors in the past, today more and more are being awarded as packages where the organisational whole of the entire project is missing. The idea of building logistics developed in these kinds of situations as an independent trade that wants to further evolve the industrialisation of construction sites. The vision: to establish working conditions as found in the well organised production processes of stationary industry.
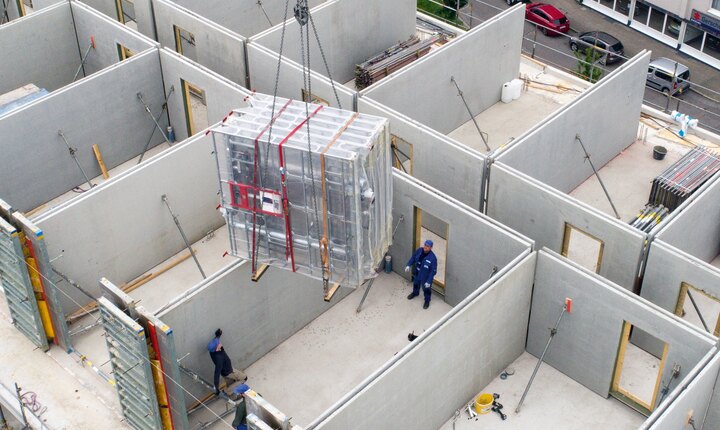
Building logistics is oriented towards the commercial definition of structural and procedural organisation: codes of conduct and a logistics handbook are becoming contractual elements for all companies on the building site. High up among the duties of the building logistics manager as a neutral instance for all participating companies is access control. Each person involved in the construction receives an ID with a chip and is recorded entering and exiting the site. This also allows the prevention of undocumented work and all data is ready to hand during routine inspections by customs. An app issues time slots for each delivery and disposal so that suppliers don't interfere with one another.
Disposals from the building site are also tightly monitored via a centrally organised waste point. The costs are billed directly to the companies so they profit from the savings brought by good waste separation. Naturally, this only functions with a good degree of monitoring, hence this forms part of the building logistics manager's duties.
Organising up to 200 trucks a day
Instances like this on the construction site are not a fiction these days. The industrial and organisational researcher Andreas Goetz – a lateral entrant when it comes to construction and a pioneer in building logistics – has been tackling the development of this new trade for some 20 years. His ideas resulted in web-based organisational tools for the control of material flows. Or in a disposal system with lockable rolling containers. Today, he works primarily as a consultant for constructors and supports large building sites.
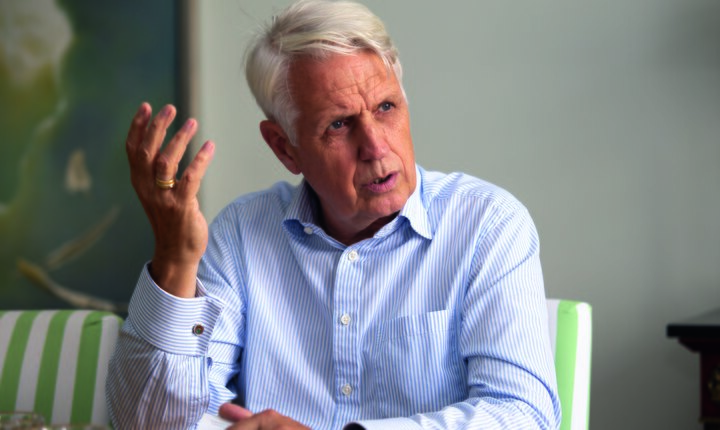
The logistics specialists only accounts for around three percent of the construction costs, depending on the scope of their service package. This still leaves a significant net benefit.
The importance of bringing in the logistics specialist as early as possible is demonstrated for example with the PalaisQuartier project in the city of Frankfurt. Based purely on logistical reasons (here: a lack of space on the premises), two ceilings for the basements in SLW 30 were expanded to make them passable for HGVs. All deliveries and disposal transports were handled in these spaces – up to 200 trucks a day during development. The costs of organisational deficiencies are hard to quantify. Goetz estimated the savings in a thesis that ran into significant double figures. “The logistics specialists only accounts for around three percent of the construction costs, depending on the scope of their service package. This still leaves a significant net benefit.” Other advantages include lower environmental and noise impacts as well as a reduced number of construction delays.
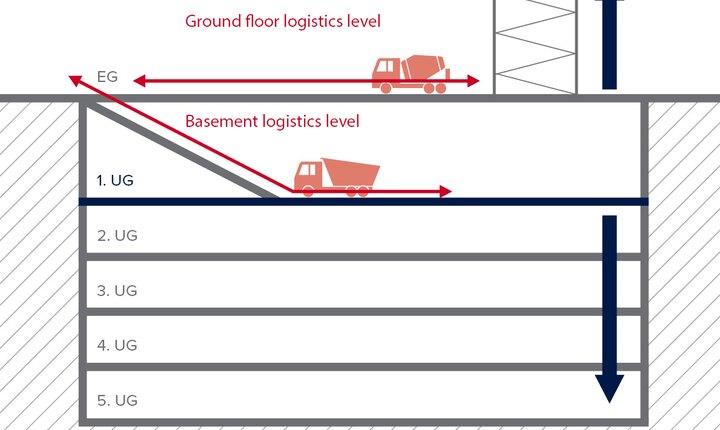
What can the construction industry do to optimise building logistics and take advantage of it? For Goetz it's the industrial prefabrication of components such as sanitary walls, installation shafts but also entire room systems that reduce the complexity of construction site workflows, avoid errors and provide additional efficiency: “There is still lots more potential to be exploited here. It comes down to close cooperation between the architect, planner and manufacturer”.
When does the logistics provider start paying off?
According to experience values, integrating building logistics as an additional trade pays off after a construction volume of approx. 30 million euros; the ideas should flow into every building development, however. In order to make a decision, the responsible parties should pose the questions of whether and how they want to overcome the following problems with consideration to the construction site environment as early as possible:
- Prevention of illegal employment via access controls
- Monitoring and prevention of thefts
- Transparency of all logistical processes
- Lay-out planning for the building site in all construction phases
- Control of material flows and storage
- Distribution of infrastructure such as unloading areas, cranes and machines
- Waste disposal with the cleanest possible separation
- Cleanliness and monitoring of work safety
- Billing of the central logistics services employed