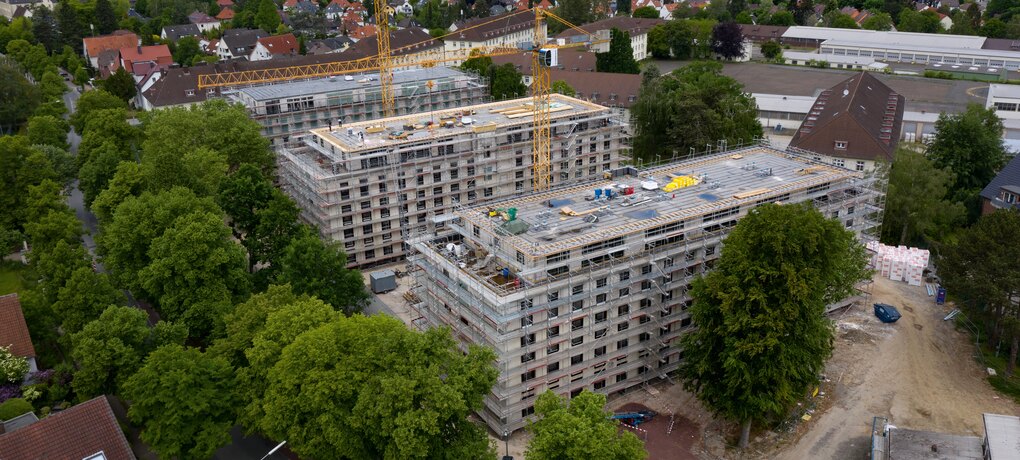
System decisions affect the entire life cycle
For some time there has been a certain tradition of assessing buildings over their entire life cycle. As early as the late 1990s, Prof. Fritz Steimle from the University of Essen gave a lecture on the energy consumption of buildings with air conditioning – usually commercial buildings with offices or sales areas. According to him, this kind of building consumes 80 percent of the total energy expended over its useful life. The planning and construction phase should account for around 15 percent of the energy consumption and the demolition will ultimately have an impact of around 5 percent. Steimle’s conclusion, which matches the current perspective: if you want to take efficiency measures, you should start with heating and air conditioning.
Today, highly efficient heating and air conditioning technology is mandatory, and this shifts the relationship between construction, operation and demolition. The graphic on page 9 shows the distribution of the amount of energy in the left column as described above – the middle, light blue area for the operation of the building clearly dominates the overall energy requirement.
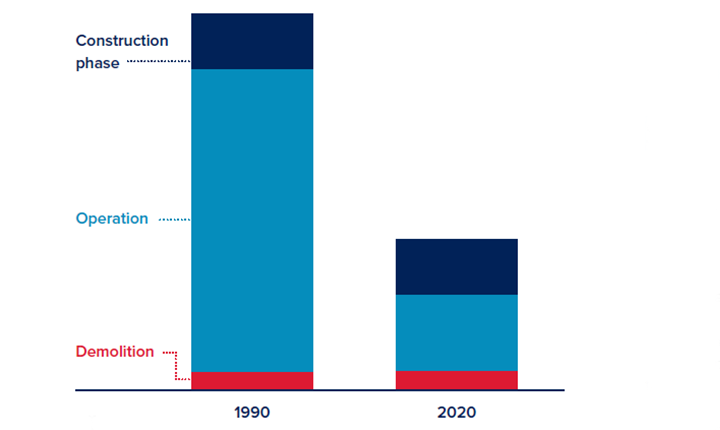
On the right is a comparison column for energy consumption that has been reduced to a quarter over the life of the building. This means that today's technical possibilities in terms of energy efficiency would still not be exhausted – just think of zero or even plus energy buildings that produce more energy than they consume over their lifespan by generating renewable energies. Of course, this only works if appropriate system decisions are made in the very early phases of building planning – for example, whether and how the extraction of ambient heat for heat pumps can be designed on site.
The graphic shows another effect: Not only has overall consumption decreased, the ratio has also changed to a large extent: the planning and construction phase in particular is much more important today. It is therefore all the more important to take a critical look at this area.
A range of assessment procedures
The modern consideration of buildings over their life cycle is not limited to the energy demand. An example of much more differentiated procedures is the DGNB system of the German Sustainable Building Council, which has been offering certification procedures for new and old buildings as well as for renovations and demolitions since 2009. It is not just ecological and economic qualities that are assessed. Criteria are also incorporated that are based on user needs – from thermal comfort and noise protection to location quality, in which, for example, transport connections are assessed. Depending on the quality of the building, certificates are awarded in platinum, gold, silver or bronze. Other systems are also widespread in English-speaking markets, such as the LEED method in the USA or the BREEAM method, which was the first certification method to be developed in England. These certifications target the entire life cycle of the building.
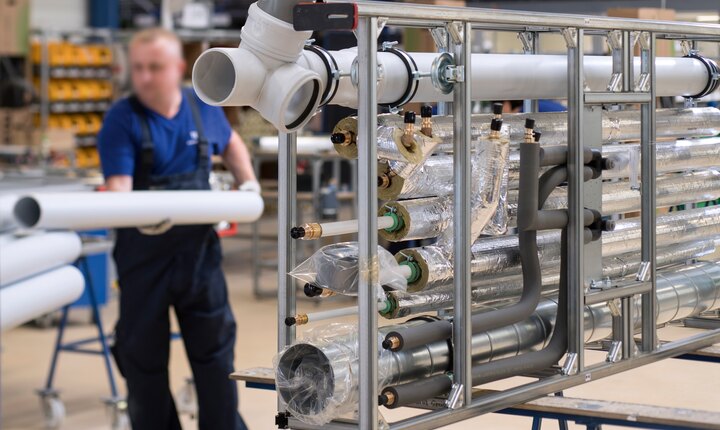
quality standards that would barely be possible under construction site operations.
System decisions in the early planning phases
In order to meet the high demands placed on buildings – whether with or without the application of one of the above certifications – it is more important than ever for planners, architects and project developers to make the relevant system decisions in the very early project phases, because these have a major impact not only in terms of energy efficiency. According to HOAI the service phases LP2 and LP3, i.e. the preliminary planning and the draft planning,
are particularly relevant here.
As well as using renewable energies, another important system decision is the use of modular construction. The possible spectrum ranges from individual assemblies to entire rooms that are delivered to the construction site by low loader. Industrial production conditions ensure high quality and low manufacturing tolerances. The modular design also saves time and coordination on the construction site as well as logistical effort, as the industry works with large containers and uses transport packaging such as grid boxes, which significantly reduce the amount of waste. This is good for the environment, but above all the amount of small cardboard boxes and plastic packaging on the construction site is significantly reduced. Disposal costs have risen disproportionately in recent years and now account for what is no longer a negligible share of construction costs.
For building services, industrially prefabricated sanitary walls are one way of exploiting the advantages of modular construction for a building project. The sanitary technology specialist TECE offers a comprehensive service package under the name TECEsystem. This includes the planning of sanitary walls and shafts in consultation with the client, the architect and the technical building services planner, industrial prefabrication to a quality that can scarcely be achieved under construction site conditions, and delivery on the exact agreed date.
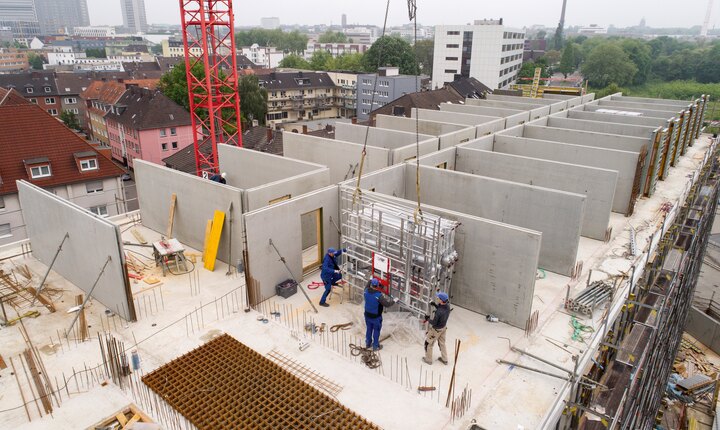
floors that are still open.
Less friction loss in the acceptance phase
In the acceptance phase, the industrial prefabrication of the sanitary technology provides further advantages. Planning and exact execution by the specialists at TECE ensure that the pre-wall construction complies with all standards and regulations in terms of potable water hygiene, fire and sound insulation. Prefabricated sanitary walls also offer advantages in later operation of the building. The TECE universal cisterns built into TECEsystem can be equipped with an integrated hygiene flush, in which a programmable, electronically controlled valve ensures the prescribed hygienic flushing of cold and hot water pipes. The flushing water is drained off via the toilet ceramics. For the housing industry, equipping the sanitary walls with the TECEprofil Geronto module is an option, whereby the bathroom can already be prepared for barrier-free renovation: Support arms and electric flush actuators can easily be retrofitted with this preparation at a later stage.
Focus on the early planning phases
The considerations regarding modular construction and industrial prefabrication show that decisions made in the early planning phases have a major impact on the construction process and, in some cases, even on the later operation of the building. Well-founded system decisions in the preliminary planning phase are just as important as a cheap or poor choice of heating and air conditioning technology.
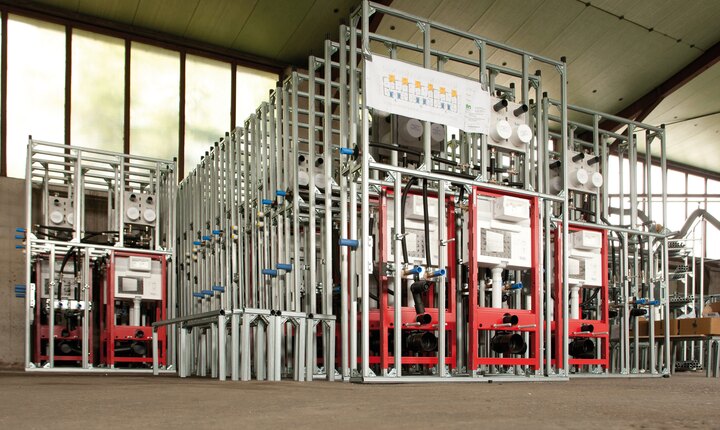