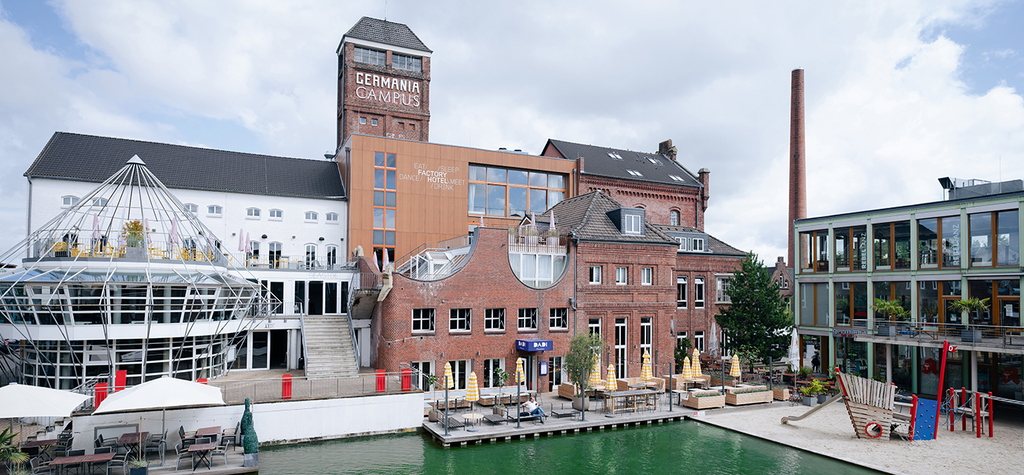
Thinking about later realisation right from the preliminary design stage
How industrially prefabricated installation walls speed up the construction process
122 furnished micro-apartments have been built on the last available building site on the Germania Campus in Münster, spread over four buildings with three to five storeys. With identical floor plans, even for the bathrooms. This is why those responsible decided to use industrially prefabricated installation walls from TECEsystem. "We already had experience of building in this way. Economically, it suited us very well," explains Markus Schulte, the architect responsible for the project at the Deilmann planning office. This is because the collaboration with TECE and Kerkhoff Gebäudetechnik GmbH - the building services contractor and "effectively our TGA planner", as Markus Schulte puts it - had already proved its worth.
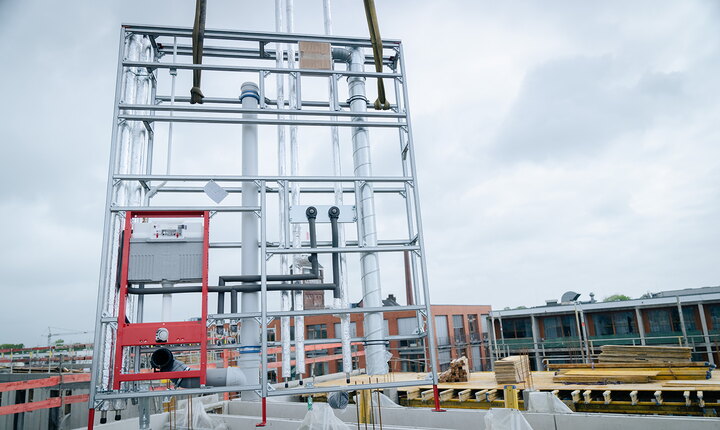
The realisation of the construction project clearly demonstrates how building with serially prefabricated elements ideally works. In the interaction of all those involved, who jointly break new ground on the construction site. The fitters only needed an hour and a half to erect and connect a prefabricated installation wall. This meant that 70 per cent of the entire sanitary installation had already been completed by the time the shell was finished.
Early cooperation in the preliminary planning phase
"In our office, we are architect, client and investor at the same time. This means that distances are short. We were convinced to work with these prefabricated system solutions in order to reduce costs and save time - although the latter also has an impact on costs, of course," says Markus Schulte.
The planning office, trades company and system provider already worked together on the preliminary planning. "You have to sit down with everyone involved at the latest in the design phase, i.e. in our service phase 3, but ideally as early as the preliminary design. In the case of the Germania Campus, we sat down together a year and a half ago. The effort involved in this early phase of the project was certainly higher, but in the end it saved us a lot of time and money on the construction site," explains Schulte.
One installation wall, two fitters, 90 minutes
TECE drew the approval drawings in the factory on the basis of the implementation plans drawn up by Kerkhoff. After approval by Alexander Lürick, project manager at Kerkhoff, the customised installation walls were then manufactured in the TECE factory. "The registers are subject to a double check - they are checked both at the factory and again by our employees after installation," he explains.
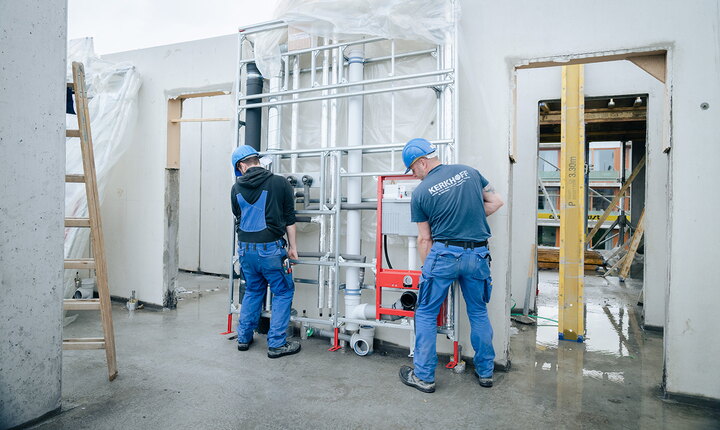
Image: Frank Peterschröder
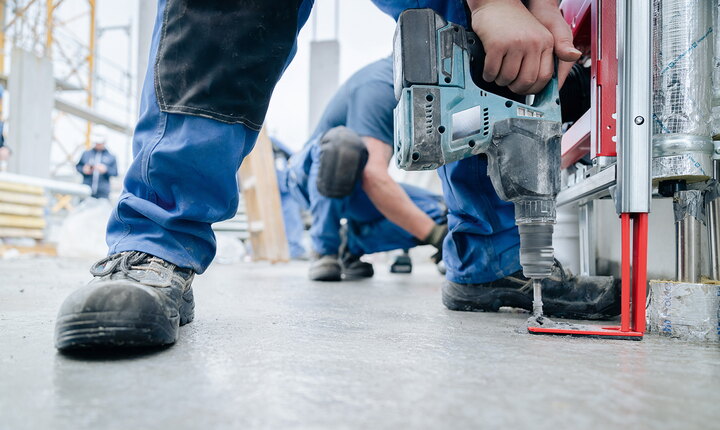
Image: Frank Peterschröder
With the help of the crane, the prefabricated installation walls were pulled as a complete package with the unloading aids to the intended floor. There, two tradesmen took over, craned the elements to their destinations, installed them and extended the pipes to the floor above. "We only need one and a half hours with two employees to assemble a prefabricated installation wall," says fitter Manuel Lammerskitten (Kerkhoff Gebäudetechnik GmbH). Project manager Alexander Lürick adds: "The assembly with prefabricated installation walls shortens our working time for a construction project with 122 micro-apartments by an estimated three months compared to conventional construction methods. Thanks to the installation of the installation ceiling in front of the respective storey ceiling during construction, we have already completed 70 per cent of the installation by the time the shell is finished."
Fire and sound insulation and warranty included
"We install our fire protection before the concrete, so it's integrated right away," says fitter Björn Vallentin. "We benefit from this during the acceptance process: the entire installation walls are tested in the factory and TECE provides a warranty for everything installed in them. We are only responsible for the floor connections and the branch lines to the kitchen and washbasin," says Alexander Lürick.
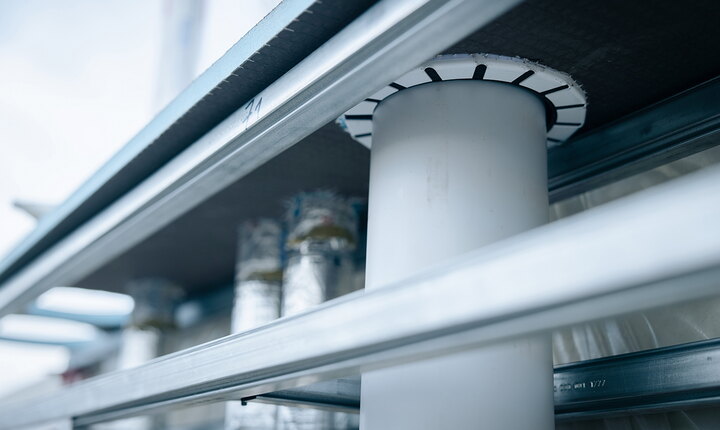
Image: Frank Peterschröder